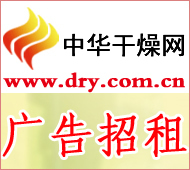
According to China Drying Technology, China's traditional technology for producing low-carbon olefins from petroleum resources is gradually losing its dominance. In the past two years, China's independent innovation and research and development of new technologies for the production of olefins from coal as raw materials have highlighted cost and price advantages, and have now become the “Xiang†of the olefin industry in China. This reporter learned from the 17th National Ethylene Annual Meeting held in Zhengzhou on September 16.
Ji Weiyi, a senior engineer of Ethylene and Aromatic Hydrocarbons at China Petroleum & Chemical Corporation, pointed out that China is a country rich in coal and lean, and coal-to-olefins is an energy strategy for China to replace coal with oil, and is one of the important ways to ensure national energy security. . For a long time, most of China's coastal oil refining and olefin integration plants or naphtha-to-olefins plants use imported crude oil or naphtha as raw materials. Although the newly-built oil refining and ethylene plants can increase the production capacity of ethylene and propylene, ethylene and propylene can be reduced. The gap, but still dependent on imports, and the degree of dependence on imports has increased year by year. Therefore, the new coal-to-olefins project that relies on its own coal resources advantage is an important strategic supplement for China's non-oil route to olefins, and it has bright prospects for development.
Zheng Qingyang, an expert with Sinopec Zhongyuan Ethylene Co., Ltd., emphasized that although China's new technology for coal to olefins has only just begun in recent years, China's independently developed coal-to-olefin technology has shown a pattern of wind, water, and flowering. The DMTO technology developed by the Dalian Institute of Chemical Physics of the Chinese Academy of Sciences with proprietary intellectual property rights is used in China's first annual production of 1.8 million tons of methanol and an annual output of 600,000 tons of coal-to-olefins industrial demonstration devices. In the commercial operation of Baotou Baotou, the methanol conversion rate reached 99.9%, and achieved very good economic and social benefits. The methanol-to-olefin technology (SMTO) jointly developed by Sinopec Shanghai Petrochemical Research Institute and China Petrochemical Engineering Design Institute has achieved 100 tons of Nissan in Beijing Yanshan Petrochemical Company and Zhongyuan Petrochemical Co., Ltd. in 2011 respectively. Methanol to olefins pilot plant and an annual output of 600,000 tons of methanol to olefin industrial equipment stable operation. The fluidized bed methanol conversion propylene technology (FMTP) jointly developed by China Chemical Engineering Group, Tsinghua University and Huaihua Group achieved an FMTP pilot test with an annual processing capacity of 30,000 tons of methanol. In 2009, it fully opened up the system process. Process. It can be seen that the new technology of coal-to-olefins developed by our country's independent innovation has matured, and its project technical level and industrialized production scale are at the leading international level. These new technologies have laid a solid foundation for the promotion, application and industrialization of coal-to-olefins in China in the future.
In 2012, affected by the two factors of sharp increase in raw material costs and sluggish market demand, the gross profit rate of 25 sets of naphtha cracker-to-olefin plants across the country dropped drastically, and even in the second quarter, there was a total loss. Most ethylene plants are now in production. It is also in a reduced load operation. However, the equipment for producing olefins from coal-to-olefin process technology has risen suddenly. The methanol-to-olefin products of Shenhua Baotou Coal Chemical Company have turned against the market, and the ethylene cost per ton is 2,000 yuan lower than that of the traditional naphtha cracking process. This was achieved in the first half of this year. The profit was 610 million yuan.
According to Jin Haifeng, an expert from China Shenhua Group Baotou Coal Chemical Company, in the next 3 to 5 years, the coal-to-olefin technology plant will occupy half of China's olefin industrial plants. According to incomplete statistics, within the past 3 years, the domestic coal-to-olefins plant to be started construction may break through 36 sets (including the equipment being tested). Most of these coal-to-olefins plants are planned to be built in the coal provinces of western China. At that time, the new technology of coal to olefins will completely change the pattern of China's olefin industry, "the east is rich in poverty." It is understood that there are 7 projects planned to be built in Inner Mongolia, 7 in Shaanxi, 4 in Xinjiang, 3 in Ningxia, 3 in Shanxi, and 2 in Henan, and Anhui, Guizhou, Shandong, Gansu, Zhejiang, Liaoning, Dalian, and Qinghai. The province is also doing the preliminary work of the coal to olefin project. Among the above-mentioned investment project establishment units, China Shenhua, China Coal Group, Datang International, Sinopec and Pucheng Clean Energy Chemicals have exceeded the annual production capacity of 1.8 million tons of methanol and 600,000 tons of polyolefins. With regard to the scale of the equipment, it is expected that the number of new technology units for coal to olefins that will be completed and put into operation in China in the next 3 to 5 years will exceed the number of existing naphtha cracking and olefin production equipment in China.
In addition, in the face of the current explosive situation in the domestic coal-to-olefins new technology project construction, some experts have also cautioned that we must pay attention to the CO2 emission treatment and the conservation and utilization of water resources to ensure that the new technologies for coal-to-olefin production in China will move towards health and speed. Orderly development.
Bridge Plug,Retrievable Bridge Plug,Api Bridge Plug,Cast Iron Bridge Plug
Henan Dongfanglong Machine Manufacture Co., Ltd , https://www.dfloilm.com