Model NO.: KXD-panel
Delivery: 60days
Voltage: 308V 50Hz 3phases
Warranty: 1 Year
Weight: 17.5 Tons
After Sales Service: Engineers Available to Service Oversea
Brand: Kexinda
Trademark: KXD
Transport Package: by Sea
Specification: 4500mmx2500mmx2600mm
Origin: China
HS Code: 84552210
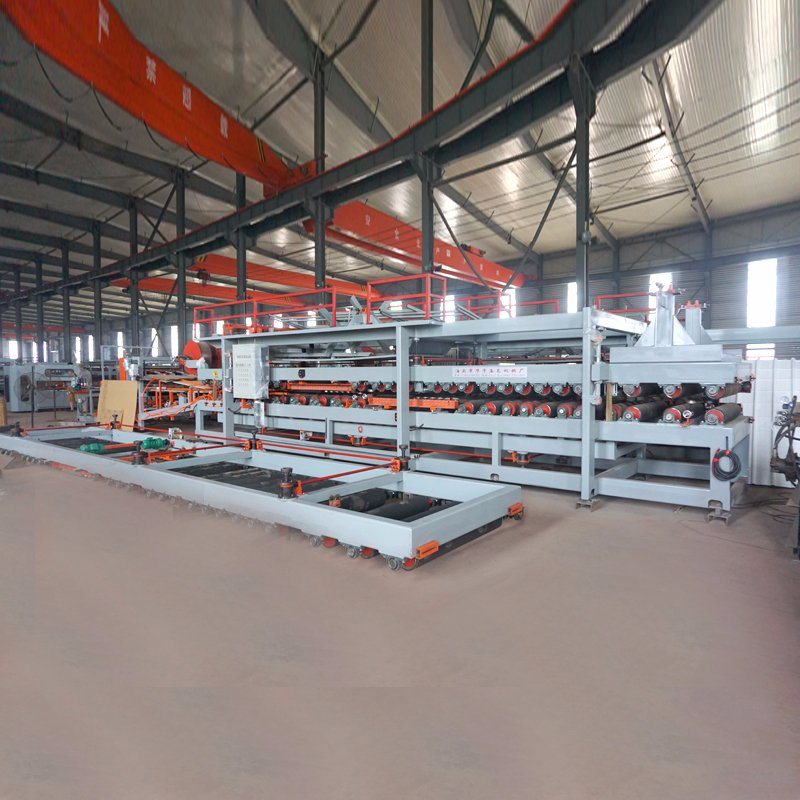
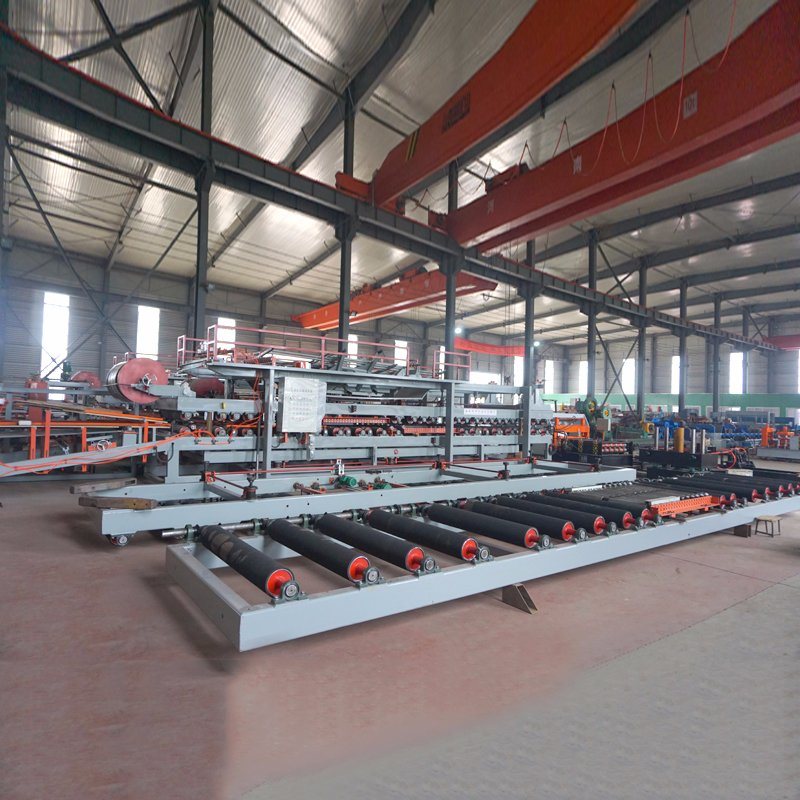
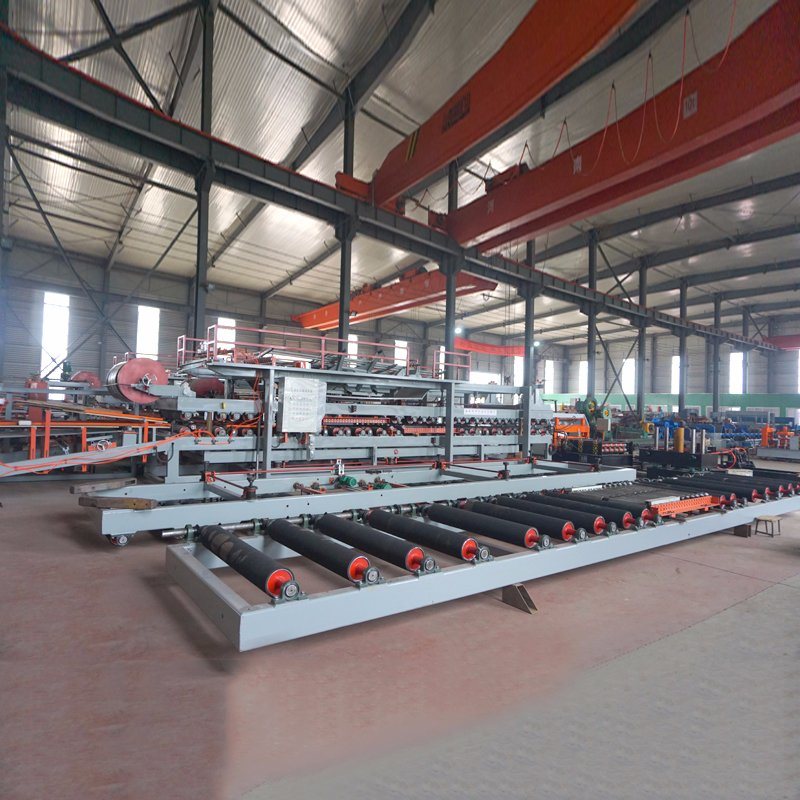
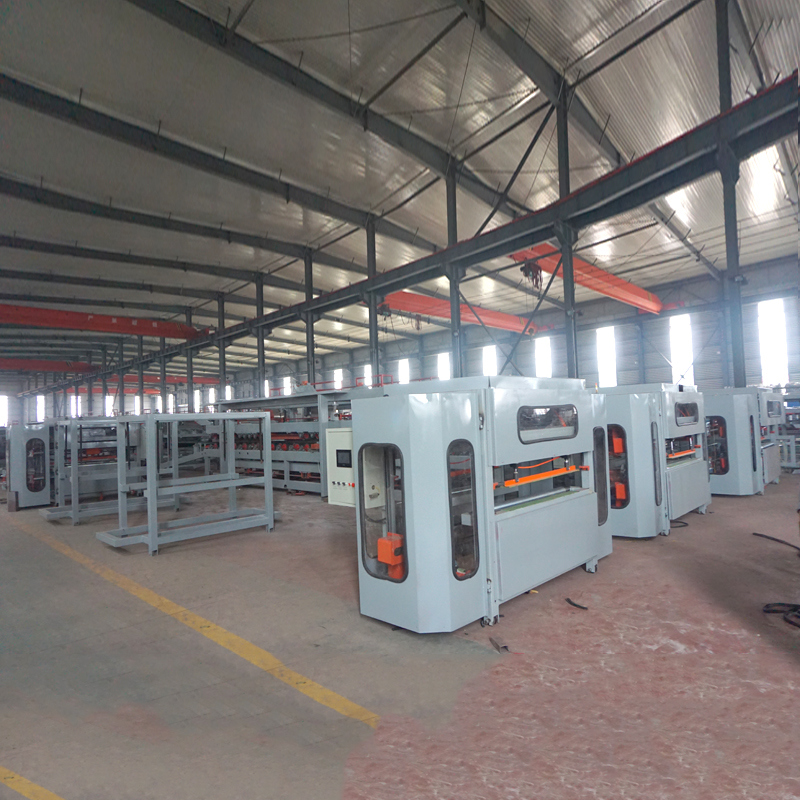
Colored Steel Sandwich Panel Production Line mainly consists of the Corrugated Roll Forming Machine and the Colored Steel Sandwich Panel Laminator. With this machine colored steel wall panels or colored steel roof panel can be produced in just one-time, and the Corrugated Roll Forming Machine and the Sandwich Panel Laminator can work independently. The whole production line of the Corrugated Roll Forming Machine consists of the uncoiler, cold-bending roll forming machine, cutting device, whereas the Sandwich Panel Laminator consists of the uncoiler for colored steel, EPS block, or mineral wool panel, shallow wave for wall panels pressing device, extruding system, mixed-glue spraying, heating and pressurizing system, sandwich, flat curling, edge rolling, edge-turnover, grooving, edge-trimming device, pneumatic clamping device, automatic plastic film coating device, automatic cutting, product stacker ;
2. The transmission of the sandwich panel laminator uses worm-worm gear transmission system, ensuring that lamination speed is stable and lamination is uniform ;
3. The sandwich panel laminator uses the frequency regulator to automatically cut according to the pre-set sandwich panel length ;
4. The sandwich panel laminator uses rubber-coated roller type laminator to protect the color paint on the colored steel as well as during the pressurizing of the sandwich panel ;
5. The sandwich panel laminator has a high quality and thick wall rectangular steel welding method, and to get rid of the rust, polishing, smoothing and aging treament ;
6. The appropriate colored steel sheet: width=1000-1200mm (the size of the length of panel is without imitation), thickness= 0.2-0.8mm ;
7. The recommended core materials for Sandwich Panel: EPS Panels, PU Panels, XPS Panels and Mineral Wool Panels;
8. Production Capacity of this Production Line: 5-7m/min; Total Length of this Production Line: 60m; Net Weight of this Production Line: About 30tons; Total Power Supply of this Production Line: 60kw; Thickness of the finished Panel produced by this production line: 50-250mm.
----------------------------------------------------------------------------------------------------------------------------------------------
EPS(Expanded polystyrene), well known as Styrofoam, is a good thermal insulation with waterproofing. Also, it can be recycled. However, the biggest selling point is a low price.
Our EPS sandwich panel line is a fully automation equipment system to produce various shapes of sandwich panels continuously and efficiently using EPS as a core material.
Â
KEXINDA's EPS sandwich panel line is composed as follows;
Â
Composition
Step 1. | Decoiling system |
Step 2. | Roll forming system |
Step 3. | EPS board feeding system |
Step 4. | Adhesive(glue) system |
Step 5. | Laminating system |
Step 6. | Cutting system |
Step 7. | Cooling system |
Step 8. | Stacking system |
Step 9. | Wrapping system |
Â
Our expanded polystyrene sandwich panel production line(EPS sandwich panel line) is already recognized its value by major sandwich panel producing companies at domestic and foreign with various technical researches and a high level services, KEXINDA, we will keep trying for development in accordance with customer's needs for the high quality sandwich panels.
Â
Specification
Kind of products | Â Interior wall, Exterior wall(Secret fix), Corrugated roof and more |
Density of core material | Â Standard 15K |
Production speed | Â Average 4~18m/min |
Annual capacity | Â About 800,000 |
Necessary dimension |  Approximately W15m x L80m x H7m |
Required electric power | Â About 150kw |
Required air pressure | Â Minimum 6~7bar |
Composition
- Mineral-wool &Â PU/PIR combined sandwich panel production line
Step 1. | Decoiling system |
Step 2. | Roll forming system |
Step 3. | Mineral-wool board feeding system |
Step 4. | Adhesive(glue) system |
Step 5. | Side PU injection system |
Step 6. | PU/PIR foaming system |
Step 7. | Double belt slat conveyor(caterpillar) system |
Step 8. | Cutting system |
Step 9. | Cooling system |
Step 10. | Stacking system |
Step 11. | Wrapping system |
- EPS &Â Mineral-wool combined sandwich panel production line
Step 1. | Decoiling system |
Step 2. | Roll forming system |
Step 3. | Mineral-wool board feeding system |
Step 4. | EPS board feeding system |
Step 5. | Adhesive(glue) system |
Step 6. | Side PU injection system |
Step 7. | Cutting system |
Step 8. | Cooling system |
Step 9. | Stacking system |
Step 10. | Wrapping system |
Â
Our combined sandwich panel production line is already recognized its value by major sandwich panel producing companies at domestic and foreign with various technical researches and a high level services, KEXINDA, we will keep trying for development in accordance with customer's needs for the high quality sandwich panels.
contact with Roy Gao to discuss the order,
Â
0086 159 3271 2693
Â
Â
Â
Â
Â
Â
Sandwich Panel Roll Forming Machine
Sandwich Panel Roll Forming Line
Eps Sandwich Panel Line
Mineral Wool Sandwich Panel Line
Sandwich Panel Roll Former
Composite Panel Roll Forming Line
Cable Tray Roll Forming Machine/Cable Ladder Forming Machine could suuport the following types of Cable Tray Systems: Aluminum , Mill Galvanizied Steel , Hot-Dipped Galvanized Steel , Stainless Steel, Fiberglass , PVC Coated , Single Rail , and Wire Mesh Wire Basket cable trays. Our cable tray systems meet or exceed all the NEMA, UL, CTI, and CSA standards and are utilized in nearly every industry. Our roll forming machine could work speed 25m/min.
Cable Tray Roll Forming Machine
Cable Tray Roll Forming Machine, Cable Ladder Roll Forming, Cable Tray Making Machine, Steel Cable Tray Roll Forming Machine,Cable Ladder Forming Machine
Zhongtuo Roll Forming Machinery Co., ltd , https://www.frameforming.nl