- Material: Stainless Steel
- Power: Electric
- Specification: SGS, ISO9001
- Structure: Multistage Pump
- Trademark: AOLI
- Origin: China
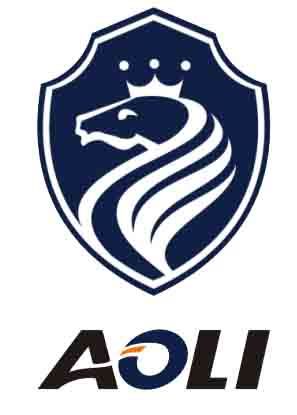
DG Boiler Feed Water Pump Features and benefits
Low noise
Stable running
DG Boiler Feed Water Pump Applications
Boiler water supply
DG Boiler Feed Water Pump Technical Data
Diameter 40~200mm
Flow 6.3~280m3/h
Head 75~650m
Fluid Temperature -45C~+420C
Operation Pressure ≤30bar
DG Boiler Feed Water Pump Material:
Cast iron: 80 degree
Nodular cast iron: 150 degree
Cast steel, Stainless steel: 200 degree
The data above is a part of our products,we can choose the perfect pump for you according to your requirements.
Â
Please feel free to contact us if you have any question.
Â
Contact Details:
Â
David Song
Â
Sales Manager
Â
Tel: +86-21-39170017(direct), Fax: +86-21-39170010
Â
Mob: +86-(0)13816987562
Â
Casting Polyurethane Prepolymer
Casting Polyurethane Prepolymer used for making wheels, Sieve, machinery parts, sealing ring, PU rollers and other elastomers.
We provide customized products , polyester and polyether in PTMEG/PPG based materials
Casting polyurethane prepolymers involves a process where a liquid mixture of polyols and isocyanates is poured into a mold or container and allowed to cure or solidify. This process is commonly used in various industries such as automotive, construction, and manufacturing.
Here is a step-by-step guide on how to cast polyurethane prepolymers:
1. Prepare the mold: Clean the mold thoroughly and ensure it is free from any debris or contaminants. Apply a mold release agent to facilitate the easy removal of the cured polyurethane.
2. Measure and mix the components: Measure the desired amount of polyol and isocyanate components. The specific ratio will depend on the desired properties of the final product, which can be found in the product's technical data sheet. Pour the measured components into a clean mixing container.
3. Mix the components: Use a mechanical mixer or a high-speed drill with a mixing attachment to thoroughly mix the polyol and isocyanate components together. Make sure to mix for the recommended amount of time specified by the manufacturer to ensure complete homogeneity.
4. Degassing: After mixing, it is important to degas the mixture to remove any trapped air bubbles. This can be done by placing the mixture in a vacuum chamber and applying vacuum pressure for a specified period of time. Alternatively, a vacuum degassing unit can be used.
5. Pouring the mixture: Once the mixture is properly degassed, pour it into the prepared mold or container. Take care to avoid introducing any additional air bubbles during the pouring process.
6. Curing: Allow the poured mixture to cure at room temperature or, if necessary, in a temperature-controlled environment. The curing time will vary depending on the specific polyurethane prepolymer used and the desired hardness or flexibility of the final product. Follow the manufacturer's recommendations for curing time and temperature.
7. Demolding: After the polyurethane has fully cured, carefully remove it from the mold or container. Use caution to prevent any damage to the cured part.
8. Post-curing (optional): Depending on the specific polyurethane prepolymer used, post-curing may be required to optimize the material's properties. This can be done by subjecting the cured part to elevated temperatures for a specific period of time.
It is important to note that casting polyurethane prepolymers requires proper safety precautions, such as wearing appropriate personal protective equipment (PPE) and working in a well-ventilated area. Always follow the manufacturer's instructions and guidelines for handling and working with polyurethane prepolymers.
Good Wheel Polyurethane Prepolymer,Casting Polyurethane Prepolymer,Casting Pu For Elastomers,Custom Polyether Polyurethane Prepolymer
XUCHUAN CHEMICAL(SUZHOU) CO., LTD , https://www.xuchuanpu.com