First, the valve positioner working principle Valve positioner as one of the main components of the control valve, which mainly play an important role in the control and regulation of the valve. The adjustment mechanism is to feedback the position of the valve stem to the control unit of the valve positioner to achieve a closed loop control, so that the valve position control is more accurate. The main principle is as shown in Figure 1:
Second, the development process of valves at home and abroad The development of the valve locator has experienced the development process from traditional to ordinary, and then to the modern regional bus valve positioner. The traditional valve positioner is mainly based on pneumatic valve positioners. With the development of science and technology, the emergence of the micro-controller processor makes the micro-controller processor apply a large valve controller, forming a preliminary preliminary intelligent valve positioning. With the advancement of science and technology and the advancement of industrial control, modern valve positioners and more advanced intelligent algorithms combine to set parameters in the installation process. This makes installation easy and valve positioning possible. The commissioning and maintenance of the device is also easier, resulting in an advanced and more sensitive controller.
Due to the early industrial revolution in foreign countries, after a period of development and progress, advanced valve positioner manufacturing companies including Siemens in Japan and Fisher-Rosemont in Germany have been formed. Their research results represent the In the future, the development of valve science and technology, at the same time, the market share of valve locators they have developed in China accounts for half of China's market share, and many of their varieties are widely accepted and applied by the international community. Such as Zhong SHH. "Research and Development of HVP Series Smart Valve Positioner." published in the article proposed that now abroad has begun to study a model of artificial intelligence modeled on artificial intelligence, which is mainly the use of its time-varying and non-linear Features. Foreign countries have moved from intelligence to artificial intelligence in the study; Shang QL, Jiang P "Research on Intelligent Elec-troPneumatic Valve Apparatus" pointed out that the application of intelligent electronics in the valve positioner. Through the application of this technology, it is possible to realize the convenience and more rapid intelligence of the control system. Through the automatic adjustment and setting of parameters, many manual operations are reduced.
China is relatively late in the production of valves, leading to China's relatively backward production of valves. After China's accession to the WTO, Chinese enterprises began to make up for the technological gap on a large scale by introducing advanced production technology, and at the same time attracting outstanding technical talents from abroad to come to China to research and develop the design of the valve locator to our country’s The gap in the development of the valve positioner has been greatly reduced. Researchers in China have conducted profound research and analysis of valve positioners and formed research results. In his paper published in 2009, Nie Shaozhong introduced the design of an intelligent valve positioner, which uses a human-like intelligent control method capable of handling non-linear and time-varying objects well. The main control unit of the valve actuator is located on the intelligent valve positioner. During the application process, the humanoid intelligent controller can adjust the control parameters through self-detection, and can identify the characteristics of the valve and pass certain compensation methods. In order to achieve the blocking of the gas leakage phenomenon, the simulation results are shown in the paper, which shows the applicability of the human intelligent algorithm. Yang Weiqing and Wang Huaxiang introduced the hardware system and software design of a two-wire intelligent electric valve positioner based on the HART protocol in the "Parameter self-tuning of intelligent electric valve positioner" published in 2010, focusing on the self-tuning of the parameters of the system. By adopting a piecewise linearization method, the parameter self-tuning process is improved, so that the system can automatically identify the parameters required for optimal control, for example, the state parameters such as gas leakage measurement and identification optimization can be applied to the control valve. Accuracy and speed play an increasing role. Fu Jian pointed out in the “HVP Smart Valve Positioner Design†published in August 2013 that low-power, high-reliability networked intelligent valve positioners have become an important component of pneumatic actuator control valves. A design proposal using multiple independent intellectual property rights was proposed, and a smart valve positioner was developed accordingly.
Third, the valve positioner control algorithm research status Valve can be classified according to the different driving methods, which are mainly divided into three types, which are pneumatic, electric and hydraulic valves. Among them, the application of pneumatic valves in industry is relatively large. This is because it has many advantages. For example, the structure of pneumatic valves is relatively simple. At the same time, it can prevent explosions and fires. It does not require high technicality and is very convenient to use. reliable. This article mainly discusses the pneumatic intelligent electric valve positioner. Its control algorithm is as follows:
(1) Conventional PID control. The principle of the PID control algorithm is that the determination of the control quantity is determined by the system error, its integral and differential, and then the result obtained by a factor. This is currently a commonly used control algorithm, but there are certain deficiencies, for example, Because of the nonlinearity and time-varying characteristics of the actuator control, the control accuracy is low, and it does not have good dynamic performance and robustness.
(2) State-based compensation control. Pneumatic actuators have the disadvantages of non-linearity, time-varying, hysteresis, etc. In addition, there will be some clearance and friction when the pneumatic actuator is executed, which will have a certain influence on the effect of the control, and pass through the state quantity of the pneumatic actuator. Observations are made and compensated for by certain means. For example, the friction compensation method is used to compensate for the hysteresis characteristics of the pneumatic actuator and a good control effect can be achieved.
(3) Predictive control. Some industrial production processes are more complex and difficult to describe using precise mathematical models. In this case, they can be controlled using predictive control algorithms. Nowadays, predictive control algorithms are applied to control systems used in many fields such as electric power, petroleum, and machinery. There are many models of prediction algorithms, among which are the prediction models of pneumatic actuators based on fuzzy inference. The prediction algorithm also has some defects, mainly reflected in its low control accuracy, and the anti-adjustment method in control feedback is relatively single.
(4) Sliding mode control. Sliding mode control algorithm makes a non-continuous and non-linear control algorithm with certain robust characteristics. The control process is the process of continuous conversion of different control logics, but when using this control algorithm to control the pneumatic actuator, With a certain inertia and time lag, this can lead to suppression of chattering. (See Table 1)
Fourth, the application of fieldbus technology in the valve positioner The development of fieldbus technology has promoted the continuous improvement of the intelligent valve positioner, which has led to the change of the intelligent valve positioner control system, and is different from the traditional control form. It integrates control modules, IO modules and other functional modules into intelligent field devices, and connects intelligent field devices, positioners, actuators, and measuring instruments through a communication cable to form a fieldbus network, which greatly enhances The timeliness of the control of the intelligent control system can also achieve a more decentralized control of different devices. Practically field devices in the fieldbus control system and the need to comply with the provisions of the bus standard in order to achieve signal transfer matching. The development of fieldbus is based on the rapid development of smart instruments. Nowadays, there are many types of fieldbus, such as HART, PROTIBUS, and FOUNDATION fieldbus.
HART is a fieldbus technology solution with compatibility. It can realize the advantages of the bus service, and can also be compatible with the 4-20mA system that still exists. The protocol followed is the HART protocol, which is a transitional protocol. The process of converting the simulated system to digitization and informationization is also compatible. Intelligent instruments based on the HART protocol are characterized by low cost, high precision, and easy maintenance. Therefore, they are widely used in the market and their market share is relatively large. It is speculated that the HART protocol will be used for the next 15 to 20 years. Therefore, its application space is relatively broad. The combination of fieldbus and intelligent digital valve positioner based on HART protocol is the trend of future development. However, due to the late start of industrialization in our country, there is not enough research on smart valve positioners, and there is a certain degree of backwardness compared to western countries. Therefore, China should actively promote the research and production of relevant intelligent products.
Rotary Damper with gear. Gear Damper is used to dampen drives, control speed, and many other applications. Gear dampers are widely used in automobile interior decoration, household electric appliances,etc. Gear damper increasing equipment life and reducing maintenance expenses.
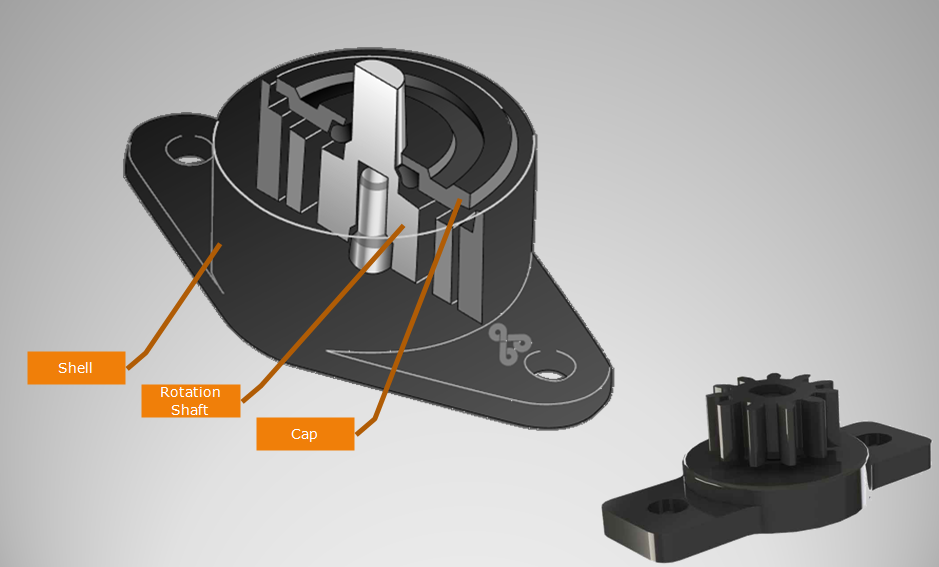
NOTE:
1. Please contact the corresponding product engineer for specific torque products.
2. Max. rotation speed: 50r/min
3. Max. circle rate: 6 cycle/min(Clockwise360 °, 360 ° anti-clockwise for 1 cycle)
4.Operating temperature: -10~50℃
5.Storage temperature:-30~80℃
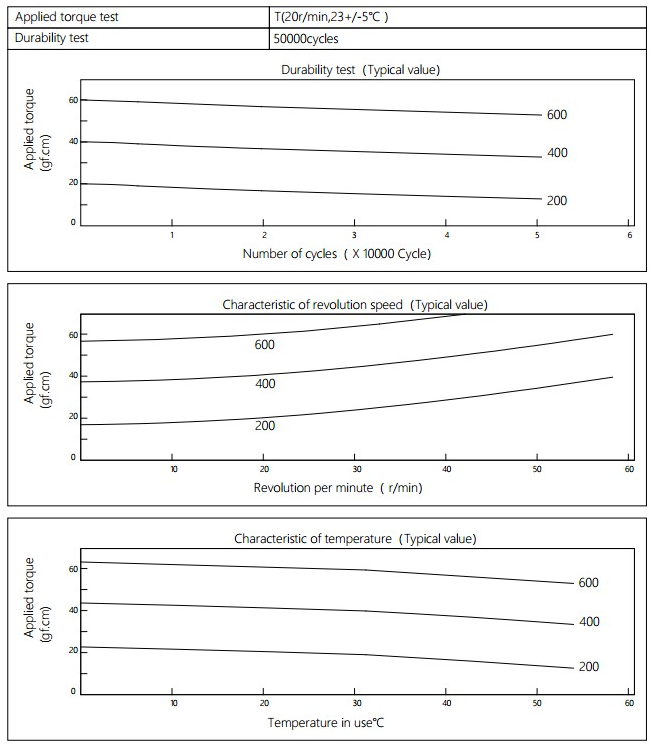
Applied torque: (T)
Test Temperature: 23+/-5℃
Rotating speed:20r/min
Durability test Method: Clockwise 360 °, 360 ° anti-clockwise
Rotating speed:20r/min
Test Frequency: 1cycle/min
Test Temperature: 23±5℃
Durability test cycle: 50000cycle
Test result criteria: Store in the room temperature for 24 hours or more after the test, recording to the torque T=T±30%T.
Gear Damper
Gear Damper,Hinge Dampers,Plastic Gear Damper,Small Rotary Gear Damper,Decoration Gear Damper
Shenzhen ABD Equipment Co., Ltd. , https://www.abddamper.com