Abstract: The Zhungeer Power Plant adopts advanced Siemens optimized control software, and its software contains different functional modules.
The second phase of Inner Mongolia Guohua Zhungeer Power Plant consists of two 330 MW units. The turbine is started by the North Heavy-Alstom Medium Pressure Cylinder. The boiler adopts the Beijing-Bavaway natural circulation and the front-and-rear wall front-hedge hedge drum furnace. Thermal control using Siemens TELEPERM - XP system.
 This project is a demonstration power station in 2000. The control level should have a high starting point and a high degree of automation. In order to meet the requirements of the future electricity market, this project will focus on economic benefits under the premise of ensuring the safety of the unit. Starting from the control, advanced optimization control software will be adopted to improve the unit control, improve the efficiency, and meet the requirements of bidding on the grid. For this reason, the instrument and control system design should meet the following conditions:
 ◠With basic load operation, and with peaking capacity, to meet the controllability of power grid dispatch, and to ensure the stability of the unit.
â—Adjust the load according to the load instruction and frequency, meet the controllability of the power grid dispatch, and ensure the stability of the unit.
â—In terms of control parameters, prevent over-regulation and ensure economic efficiency. â—Guidance on the economic operation of the unit. In response to the above requirements, we plan to use Siemens' optimized control software, which contains different functional modules. We have conducted analysis and selection. The following two control modules, SR4 and PROFI, are considered suitable for our needs.
among them:
 SR4 - online optimization of unit performance  PROFl - for real-time process control, including 4 modules, the sub-sections are:
â—New unit coordinated control ◠Condensate throttling control â—Load margin forecast â—Self-study temperature control 1. SR4 function block  SR4 is the unit performance online optimization control module, which is installed in a PC, and The DCS terminal bus is connected with a separate CRT display. It extracts relevant data from the DCS system, and calculates and displays the status and efficiency of boilers, turbines, and their auxiliary engines through modeling. It provides a most economical operation mode and guides the operating personnel. operating.
 This module takes two steps, balance and simulation:
 The first step: Take 300 measurement points data from DCS and perform modeling calculation every 5 minutes to show actual performance parameters such as air precipitator leakage, boiler flue gas temperature distribution, coal consumption, condenser and heater, etc. The second step is to compare the actual system parameters with the best parameters of the simulation state, obtain the reference data, point out the deviations, and compare the economics for reference by the operating personnel.
 This method is only for online monitoring and it is not directly controlled. It can provide economic operation guidance so that the unit is in the best economic operation.
Second, PROFI function block, it contains four function blocks, it is installed in the processing module CP581 card, arranged in the DCS cabinet, Siemens TXP and CP518 connection through communication processing module CPl413 serial communication, and DCS Control systems are linked and directly involved in control.
 1) Coordinated control of new units  This approach models boilers and turbines on the basis of traditional coordinated control. Theory is based on thermal balance, feedforward control is used as a means, turbine control is used, boiler load regulation, and at the same time, the various controls The system, combined with condensate flow regulation, can achieve fast load response and combustion stabilization effects, and meet the requirements of the grid; at the same time, it can avoid the uneconomic factors brought about by achieving fast load response, fuel over regulation, and main gas throttling, thereby increasing Economical.
As shown in Figure 1.
 In this way, in terms of control, the load response can be improved, and the grid and AGC requirements can be met while maintaining the stability of the boiler and improving economic efficiency.
 2) Condensate throttling control  The main idea of ​​this method is to change the condensate flow to achieve a low increase in the amount of air extracted, so that under the condition that the main steam flow is constant, the varied amount of bleed air is applied to the steam turbine. Caused by power changes, with experts, can be within 15 seconds, the load change is 5%. In addition, in this way, the non-economical nature of the original turbine throttle adjustment load can be changed. As shown in Figure 2.
We analyze that if this method is established, this method is an ideal means of adjusting the load. This control function is for extra heat and enables the heat energy to be used for the secondary work of the turbine so that the unit can have changes in the load. The rapid response, and can further ensure the smooth and stable operation of the boiler. It can adapt to the primary and secondary frequency regulation of the power grid, which will greatly help the future unit coordination and AGC operation.
 3) Load margin prediction  This method is used to calculate the stress of boilers, turbines and pipelines, measure the magnitude of stress, and give the stress value and predicted value. Based on these values, the unit will run along the stress line, thus shortening the start-up time. Saving start-up costs can save 20% - 50%. For the hot start, it takes only half an hour from the ignition to the rated load (a Korean power plant).
According to reports, if the unit is in-depth peak adjustment (start-stop), the economic effect is better.
4) Self-learning temperature control This method is to use the mathematical model to establish different sections of the main steam system, predict the temperature, perform the state change of the smoke gas and the temperature change caused by the water spray, conduct self-learning, and establish the disturbance observer pair. Other disturbances are corrected to accurately reflect the expected values ​​of different sections of temperature. In combination with control, the temperature is quickly and accurately controlled within a narrow range. The problem of unsatisfactory adjustment quality caused by temperature delay is solved, and thermal efficiency is ensured. As shown in Figure 3.
Let us analyze that this approach is only in the adjustment of ideas, ideal than the traditional adjustment. If the model and interference factors are accurate, the effect is better.
3. The basic control performance expectation value after adopting PROFI in Zhungeer Power Plant There are two ways to improve the power plant efficiency by controlling:
1) Unit stability  Unit stability First, the characteristics of the heat boiler and the smoothness of the coal supply. Followed by the slow changes in the implementation of the entire system and temperature fluctuations. Enhancing the efficiency of power plants is mainly achieved by reducing the generation of disturbances (avoiding power sales losses), increasing unit efficiency (reducing fuel consumption per MWh), prolonging the life of expensive power plant equipment, and reducing maintenance costs.
2) Load dynamic response performance The stable unit can maintain the target load earlier and longer without operational difficulties. From a load dispatcher's point of view, this kind of power plant can provide faster and more reliable products than other power plants. If the power plant has sufficient stability to provide frequency-tuning services for the grid, this power plant is more attractive to him. The grid always needs to adjust the load at any time. This regulated unit has a very long annual power generation time and can allocate fixed costs to more MW hours than planned. Statistically speaking, his production cost per MW hours is even lower. Finally, high dynamic load response capability is the primary point of generating benefits. PROFI control is used to improve the stability of the unit and the dynamic response of the load.
Many of the benefits associated with this area are that the benefits of the area are determined by the characteristics of the equipment (eg condenser vacuum) and cannot be increased by control. But there are also some basic areas that can be used to diagnose the quality of power plant controls and can be used to provide useful indications of the desired power plant benefits. Some of them are mentioned below.
The constant load state variable  In the case that the set load value of the unit is kept unchanged for 15 minutes and the frequency is turned off once, the standard deviation of the next 60 minutes shall be obtained;
Steam temperature less than 5Kelvin
New steam pressure less than 5bar
The absolute value of 02 in the flue gas is less than 3% (02 sensor after calibration)
 No matter what the stability of the fixed-load state is, there is no significant difference in the condition of the boiler's minimum stable combustion load or 100% MCR. It is not allowed to mix fuel, change fuel quantity, or increase temperature disturbance (such as soot blowing) during the evaluation of the characteristics of the constant load state.
 Load change rate å“应 The response speed of the unit's load increase shall be 2% higher MCR per minute on the basis of the original control strategy, or it shall be at least 4% MCR/liter per minute load rate.
ç„¶ When the overshoot is exceeded, the fuel dynamic overshoot (change value of the dynamic load set point of the coal mill) should not exceed 150% of the dynamic set value of the unit load change.
When the wind-to-fuel ratio changes, the absolute deviation of 02 in the flue gas should be less than 5%. Or 2% less deviation than 02 before using PROFI scheme
When steam temperature changes, the temperature of the spray desuperheater must not exceed two or three minutes at the upper and lower limits of its operating range. Under constant load operating conditions, the total effective spray flow rate should not exceed 50% of the total steam flow.
 When the water level of the drum changes, the water level of the main steam drum should not exceed 5 times the change in water level of the drum during constant load operation, or the change amount of the steam drum should be reduced by at least 30%.
The primary frequency modulation capability should be able to freely input or withdraw one frequency modulation without obvious vapor pressure or fuel volume fluctuations, and one frequency modulation operation will not increase the chance of tripping.
 The above is Siemens optimized control software, which can be used in different control systems, simply physical.
The second phase of Inner Mongolia Guohua Zhungeer Power Plant consists of two 330 MW units. The turbine is started by the North Heavy-Alstom Medium Pressure Cylinder. The boiler adopts the Beijing-Bavaway natural circulation and the front-and-rear wall front-hedge hedge drum furnace. Thermal control using Siemens TELEPERM - XP system.
 This project is a demonstration power station in 2000. The control level should have a high starting point and a high degree of automation. In order to meet the requirements of the future electricity market, this project will focus on economic benefits under the premise of ensuring the safety of the unit. Starting from the control, advanced optimization control software will be adopted to improve the unit control, improve the efficiency, and meet the requirements of bidding on the grid. For this reason, the instrument and control system design should meet the following conditions:
 ◠With basic load operation, and with peaking capacity, to meet the controllability of power grid dispatch, and to ensure the stability of the unit.
â—Adjust the load according to the load instruction and frequency, meet the controllability of the power grid dispatch, and ensure the stability of the unit.
â—In terms of control parameters, prevent over-regulation and ensure economic efficiency. â—Guidance on the economic operation of the unit. In response to the above requirements, we plan to use Siemens' optimized control software, which contains different functional modules. We have conducted analysis and selection. The following two control modules, SR4 and PROFI, are considered suitable for our needs.
among them:
 SR4 - online optimization of unit performance  PROFl - for real-time process control, including 4 modules, the sub-sections are:
â—New unit coordinated control ◠Condensate throttling control â—Load margin forecast â—Self-study temperature control 1. SR4 function block  SR4 is the unit performance online optimization control module, which is installed in a PC, and The DCS terminal bus is connected with a separate CRT display. It extracts relevant data from the DCS system, and calculates and displays the status and efficiency of boilers, turbines, and their auxiliary engines through modeling. It provides a most economical operation mode and guides the operating personnel. operating.
 This module takes two steps, balance and simulation:
 The first step: Take 300 measurement points data from DCS and perform modeling calculation every 5 minutes to show actual performance parameters such as air precipitator leakage, boiler flue gas temperature distribution, coal consumption, condenser and heater, etc. The second step is to compare the actual system parameters with the best parameters of the simulation state, obtain the reference data, point out the deviations, and compare the economics for reference by the operating personnel.
 This method is only for online monitoring and it is not directly controlled. It can provide economic operation guidance so that the unit is in the best economic operation.
Second, PROFI function block, it contains four function blocks, it is installed in the processing module CP581 card, arranged in the DCS cabinet, Siemens TXP and CP518 connection through communication processing module CPl413 serial communication, and DCS Control systems are linked and directly involved in control.
 1) Coordinated control of new units  This approach models boilers and turbines on the basis of traditional coordinated control. Theory is based on thermal balance, feedforward control is used as a means, turbine control is used, boiler load regulation, and at the same time, the various controls The system, combined with condensate flow regulation, can achieve fast load response and combustion stabilization effects, and meet the requirements of the grid; at the same time, it can avoid the uneconomic factors brought about by achieving fast load response, fuel over regulation, and main gas throttling, thereby increasing Economical.
As shown in Figure 1.
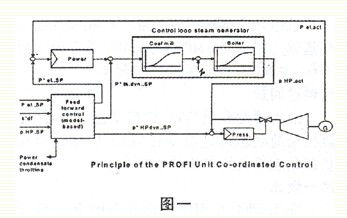
 2) Condensate throttling control  The main idea of ​​this method is to change the condensate flow to achieve a low increase in the amount of air extracted, so that under the condition that the main steam flow is constant, the varied amount of bleed air is applied to the steam turbine. Caused by power changes, with experts, can be within 15 seconds, the load change is 5%. In addition, in this way, the non-economical nature of the original turbine throttle adjustment load can be changed. As shown in Figure 2.

 3) Load margin prediction  This method is used to calculate the stress of boilers, turbines and pipelines, measure the magnitude of stress, and give the stress value and predicted value. Based on these values, the unit will run along the stress line, thus shortening the start-up time. Saving start-up costs can save 20% - 50%. For the hot start, it takes only half an hour from the ignition to the rated load (a Korean power plant).
According to reports, if the unit is in-depth peak adjustment (start-stop), the economic effect is better.
4) Self-learning temperature control This method is to use the mathematical model to establish different sections of the main steam system, predict the temperature, perform the state change of the smoke gas and the temperature change caused by the water spray, conduct self-learning, and establish the disturbance observer pair. Other disturbances are corrected to accurately reflect the expected values ​​of different sections of temperature. In combination with control, the temperature is quickly and accurately controlled within a narrow range. The problem of unsatisfactory adjustment quality caused by temperature delay is solved, and thermal efficiency is ensured. As shown in Figure 3.
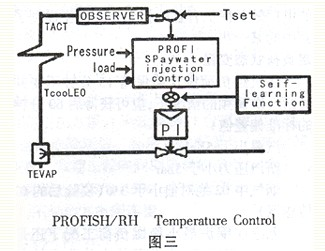
3. The basic control performance expectation value after adopting PROFI in Zhungeer Power Plant There are two ways to improve the power plant efficiency by controlling:
1) Unit stability  Unit stability First, the characteristics of the heat boiler and the smoothness of the coal supply. Followed by the slow changes in the implementation of the entire system and temperature fluctuations. Enhancing the efficiency of power plants is mainly achieved by reducing the generation of disturbances (avoiding power sales losses), increasing unit efficiency (reducing fuel consumption per MWh), prolonging the life of expensive power plant equipment, and reducing maintenance costs.
2) Load dynamic response performance The stable unit can maintain the target load earlier and longer without operational difficulties. From a load dispatcher's point of view, this kind of power plant can provide faster and more reliable products than other power plants. If the power plant has sufficient stability to provide frequency-tuning services for the grid, this power plant is more attractive to him. The grid always needs to adjust the load at any time. This regulated unit has a very long annual power generation time and can allocate fixed costs to more MW hours than planned. Statistically speaking, his production cost per MW hours is even lower. Finally, high dynamic load response capability is the primary point of generating benefits. PROFI control is used to improve the stability of the unit and the dynamic response of the load.
Many of the benefits associated with this area are that the benefits of the area are determined by the characteristics of the equipment (eg condenser vacuum) and cannot be increased by control. But there are also some basic areas that can be used to diagnose the quality of power plant controls and can be used to provide useful indications of the desired power plant benefits. Some of them are mentioned below.
The constant load state variable  In the case that the set load value of the unit is kept unchanged for 15 minutes and the frequency is turned off once, the standard deviation of the next 60 minutes shall be obtained;
Steam temperature less than 5Kelvin
New steam pressure less than 5bar
The absolute value of 02 in the flue gas is less than 3% (02 sensor after calibration)
 No matter what the stability of the fixed-load state is, there is no significant difference in the condition of the boiler's minimum stable combustion load or 100% MCR. It is not allowed to mix fuel, change fuel quantity, or increase temperature disturbance (such as soot blowing) during the evaluation of the characteristics of the constant load state.
 Load change rate å“应 The response speed of the unit's load increase shall be 2% higher MCR per minute on the basis of the original control strategy, or it shall be at least 4% MCR/liter per minute load rate.
ç„¶ When the overshoot is exceeded, the fuel dynamic overshoot (change value of the dynamic load set point of the coal mill) should not exceed 150% of the dynamic set value of the unit load change.
When the wind-to-fuel ratio changes, the absolute deviation of 02 in the flue gas should be less than 5%. Or 2% less deviation than 02 before using PROFI scheme
When steam temperature changes, the temperature of the spray desuperheater must not exceed two or three minutes at the upper and lower limits of its operating range. Under constant load operating conditions, the total effective spray flow rate should not exceed 50% of the total steam flow.
 When the water level of the drum changes, the water level of the main steam drum should not exceed 5 times the change in water level of the drum during constant load operation, or the change amount of the steam drum should be reduced by at least 30%.
The primary frequency modulation capability should be able to freely input or withdraw one frequency modulation without obvious vapor pressure or fuel volume fluctuations, and one frequency modulation operation will not increase the chance of tripping.
 The above is Siemens optimized control software, which can be used in different control systems, simply physical.
Steel Deep Drawn Parts,Hydroforming Deep Drawn Parts,Progressive Metal Stamping Car Back Lock,Stamping Tooling Metal Stamped Part
NINGBO YINZHOU HONGBO AUTOPARTS CO., LTD., , https://www.hbcarparts.com