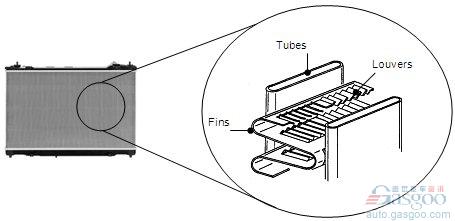
Denso said that the radiator is smaller and has greater flexibility in installation. The radiator's fins are only 16mm wide, but are comparable to the traditional 27mm wide radiators.
The efficiency of automotive radiators depends mainly on the design of the fins. Electrical installations increase the number of louver shutters, which in turn makes the new radiator about 10% more efficient than conventional radiators.
The new radiator with a fin width of 16mm will be deployed in the Lexus GS model. In order to meet the different needs of more models, Denso also plans to introduce a 27 mm wide model and a 11.5 mm wide model.
Compression molding is a manufacturing process that uses a cavity half and a core half of a mold to form material into a specific shape created by the two mold halves. Compression molds vary depending on the material being compressed and the dictates of the type of mold required.
Typically, a compression mold is mounted in a vertical press (unlike the horizontal presses that are prevalent in the Injection Molding process). Compression molding often requires that the [charge" of material be loaded into the mold, either manually or automatically, prior to the mold halves closing.
- The loss of raw materials is small and will not cause too much loss (usually 2% to 5% of the product quality).
- The shrinkage of the product is small and the repeatability is good.
- A mold with a large number of cavities can be placed on a given template, and the productivity is high.
- It can be adapted to automatic feeding and automatic removal of products.
- High production efficiency, easy to realize specialized and automated production.
- The product has high dimensional accuracy and good repeatability.
- The surface is smooth and clean without secondary modification.
- Products with complex structures can be formed at one time.
- Mass production, relatively low price.
we ever did many compression silicon parts , the hardness from 30shore A till 80shore A, colors can be customized whatever you want, we can do the compound color for you. Several free samples for the review before the overall demand running to ensure everything is clear and aligned to go. Please contact us for the professional suggestions, we have been in this field for more than 15years. thanks.
Compression Molding,Compression Forming,Rubber Compression Molding,Compression Moulding Process
Suzhou FCE precision electronics Co., LTD , https://www.sjfukeyifcesz.com