This article analyzes the packing seal of the piston compressor of Wuhan Branch of Sinopec and introduces the form of packing seal. At the same time, this paper also analyzes the failure of the packing seal failure, and proposes a solution, which provides a theoretical basis for ensuring the normal operation of the equipment.
The piston compressor is widely used because it can achieve multi-stage compression and is suitable for high pressure and low flow operation. Large-scale piston compressors have gradually been widely used, especially after the establishment of hydrogenation and hydrogen plants and reforming plants in 1996. Piston compressors have become critical equipment.
At present, Wuhan Branch's piston compressors are mainly hydrogen compressors and hybrid petroleum gas compressors. The working medium is flammable, explosive and toxic and harmful gases. Therefore, the reliability of compressor packing seals determines the normal operation of equipment. The safety and stability. Because the company has little experience in the installation and maintenance of large-scale piston compressors, and the packing forms of various types of compressors are different, there are certain difficulties in the maintenance of packing seals. In view of the above problems, the following describes the form and principle of packing seals for various types of piston compressors in Wuhan Branch, and analyzes the failure of packing seals and proposes solutions.
Packing seal form
At present, the piston compressors used in Wuhan Branch are all sealed by flat surfaces. Their stuffing boxes mainly include: a pressure-relief ring that acts as a current-limiting function; several sets of sealing rings that prevent air flow from leaking into the air vent; An exhaust control ring prevents air flow from leaking through the vent to the isolation chamber. The exhaust control ring is basically the same as the pressure relief ring of the packing, so the form of the seal ring is its main differentiation point. Its main components are a decompression ring and a seal ring.
The role of the decompression ring is to limit or control the leakage of the gas flow, mainly to reduce the role of decompression. During the suction stroke, the rapid expansion of gas from the stuffing box is prevented from flowing back to the cylinder, the pressure of the cylinder is rapidly reduced to suction pressure, and the gas in the stuffing box has a tendency to flow back into the cylinder. If there is no throttling restriction, the seal ring will open, causing premature failure or wear of the seal ring.
There are mainly two types of decompression rings, P-type and PA-type (Fig. 1). The decompression rings currently used are all P-type because the orifices of the P-type pressure-reduction ring have clearance at the ports of the ring. Sealed packing rings in piston compressors are in the form of BT, BD, BTR, TR.
The BT-type seal ring (Figure 2) is a single-acting ring that seals only one side of the pressure. It consists of a radial slit ring (on the high pressure side) and a tangential slit ring. When the radial notch is attached to the piston rod, there is still a gap in the notch so that when the compressor is running, high-pressure gas is introduced into the packing chamber, and the high-pressure gas is used to compress the packing. In addition, the radial cut ring and the tangential cut ring use the positioning pins to determine the mutual position. In order to ensure the seal, the cuts are offset from each other by an angle to prevent the gas from passing through the packing ring, and the two sealing rings are used to prevent the sealed shaft from being attached to the plane. Leakage. In addition, in order to ensure the sealing effect of the packing rings, the two rings and the piston rod need to cooperate well.
BD-type seal ring (Figure 3) is a double-acting packing ring that can seal the pressure in two directions. It is composed of two butt-joint tangential cut rings. The gaps cover each other and use the positioning pins to determine the connection position to prevent Gas leak.
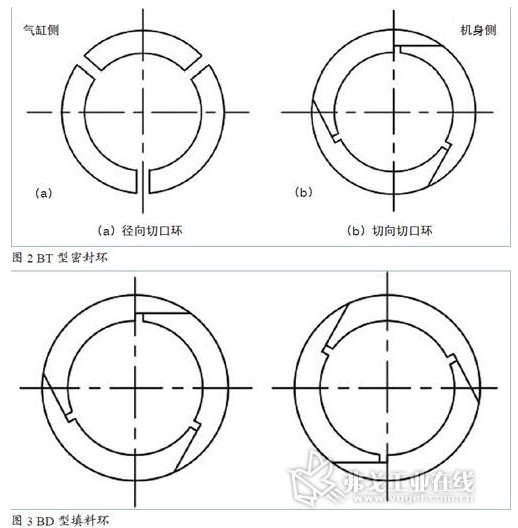
The BTR seal ring (Figure 4) consists of a non-metallic packing ring and a metal rigid ring. The BTR seal ring is suitable for high pressure compressors. The rigid ring is in the form of a radial notch. The clearance of the rigid ring port is zero. The inner diameter of the ring is slightly larger than the piston rod, and the piston rod is not tightened under the pressure (or Slightly clamping the piston rod) to prevent the non-metallic filler from being squeezed out. The role of the rigid ring is to reduce the direct impact between the tangential incision ring and the stuffing box, extending its service life. In addition, the rigid ring assists in the removal of heat from the surface of the piston rod through slight contact with the piston rod.
The TR-type seal ring (Fig. 5) is actually a variant of the BTR-type seal ring. It combines the characteristics of a tangential ring and a radial ring, which not only serves as the introduction of high-pressure gas but also serves as an axial seal. Since the tangential and radial rings are on the same ring, one leakage point can be reduced. In addition, since the seal has only two rings and the axial dimension is small, when the sealing pressure is high, the amount of leakage can be reduced by increasing the form of the stuffing box.
Seal leakage fault analysis and improvement measures
Since the inner ring of the packing ring is closely fitted to the piston rod, friction occurs between the packing seal ring and the piston rod when the device is running at a high speed, and at the same time, a large amount of frictional heat is generated, resulting in a local temperature that is too high and close to the side of the cylinder of the compressor. The temperature of the seal ring is much higher than the temperature on the body side, which can easily lead to damage of the packing seal ring and cause leakage. In order to solve the problem of seal ring failure caused by frictional heat, a part of the gas can be introduced into the surface of the piston rod by improving the sealing structure, which effectively reduces the pressure of the seal ring against the piston rod and prevents the seal ring from wearing out. In addition, the material of the seal ring is filled with PTFE, and the content of copper powder and fiber is increased in an appropriate amount to increase the heat conduction and wear resistance.
In addition to the above reasons, the leakage and improvement of packing seals mainly include the following aspects:
Packing body gasket
Packing body washers are generally made of soft metal or O-rings as gaskets. The damage of the sealing surface of the fuselage and the uneven installation force can easily cause the gasket to break, which causes the leakage of the sealing medium from the outside of the packing body to the middle body cavity. In the middle, the temperature of the middle body and the vent line increased abnormally. For the above situation, it can be eliminated by replacing parts and correct installation.
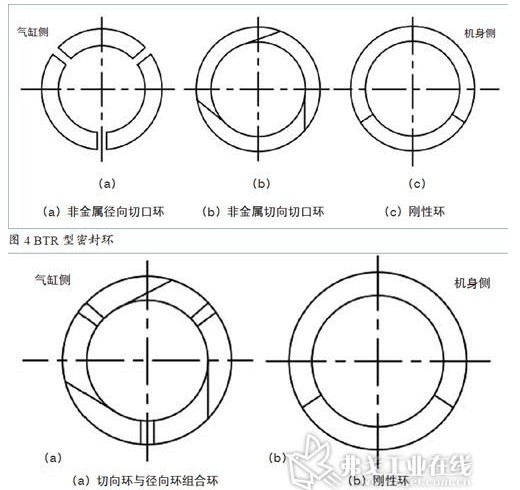
Packing box face
In the packing installation, it is required that the tangential incision ring must lie flat on the side of the groove of the stuffing box, usually due to a defect in the sealing surface of the stuffing box or a deviation of the squareness of the entire stuffing box from the piston rod, thereby causing the seal to leak. In order to avoid sealing failures in these situations, it can be solved by grinding the sealing surface of the stuffing box and adjusting the stuffing box bolts.
Packing ring
Packing ring is the most important factor causing seal leakage. Leakage of packing ring can be divided into the following aspects:
Sealing ring installed in the wrong order;
The axial gap of the seal ring is not controlled, which causes the temperature during operation to increase. The seal ring expands axially and is jammed in the stuffing box. The tangential cut-out ring seal fails.
The surface of the packing sealing ring itself is not polished satisfactorily, and the inner hole of the sealing ring and the piston rod do not fit well, resulting in leakage. Generally, the inner surface of the sealing surface can be ground to improve the fit of the sealing surface and eliminate leakage.
Sealing ring between stuffing boxes
Due to the shearing effect of the sealing ring between the stuffing boxes during installation or the aging of the sealing ring, the sealing medium gas strings are caused to cool the water and affect the sealing effect. By observing the filling cooling water sight glass, if bubbles appear, it indicates that the seal ring is defective and can be eliminated by replacing the seal ring.
Poor alignment of packing box and piston rod
When checking the leakage of the packing, the alignment problem between the stuffing box and the piston rod is often neglected. The misalignment causes a tangential incision ring and the angle between the flanks of the stuffing box to cause a leak. In order to correct misalignment between the stuffing box and the piston rod, align the piston rod with the stuffing box by adjusting the bolts of the packing body and applying appropriate torque to center the piston rod. If the concentricity between the cylinder and the slide is caused by the installation, adjust the concentricity by adjusting the cylinder support to solve the leakage problem.
The effect of external auxiliary system on the sealing effect
Cooling water
The change in temperature results in a change in the relative positions of the packing rings and piston rods, packing rings and packing boxes, packing rings themselves, which can easily cause leakage when the relative position changes. As the frictional heat causes the temperature of the packing ring to rise, the inner bore of the packing ring is deformed to disengage the piston rod, or the packing ring is separated at the tangential incision. In addition, the piston rod is curved due to uneven frictional heating, which affects the centering. In addition, when the piston rod is operated at a high temperature for a long period of time, it will exacerbate its wear and eventually lead to leakage. Therefore, it is of great significance to ensure the safe operation of the equipment by ensuring the smoothness of the cooling water of the packing and the proper flow rate.
Effect of oil injection
Too little oil in the packing seal can cause poor lubrication in the packing operation. The packing ring wears too quickly and the oil filling amount is too high. This can cause a large amount of sludge to be formed due to the worn packing and lubricant, resulting in deterioration of the lubrication condition. Therefore, the amount of oil injection must be strictly controlled.
Leakage recovery system
Leakage from the packing seal leaks through the leak recovery line. If a blockage occurs in the pipeline, it will cause the pipeline to collapse, and the leakage of the medium will be reversed, causing the leakage of the packing. Therefore, it must be ensured that the leak recovery system is unobstructed.
The piston compressor is widely used because it can achieve multi-stage compression and is suitable for high pressure and low flow operation. Large-scale piston compressors have gradually been widely used, especially after the establishment of hydrogenation and hydrogen plants and reforming plants in 1996. Piston compressors have become critical equipment.
At present, Wuhan Branch's piston compressors are mainly hydrogen compressors and hybrid petroleum gas compressors. The working medium is flammable, explosive and toxic and harmful gases. Therefore, the reliability of compressor packing seals determines the normal operation of equipment. The safety and stability. Because the company has little experience in the installation and maintenance of large-scale piston compressors, and the packing forms of various types of compressors are different, there are certain difficulties in the maintenance of packing seals. In view of the above problems, the following describes the form and principle of packing seals for various types of piston compressors in Wuhan Branch, and analyzes the failure of packing seals and proposes solutions.
Packing seal form
At present, the piston compressors used in Wuhan Branch are all sealed by flat surfaces. Their stuffing boxes mainly include: a pressure-relief ring that acts as a current-limiting function; several sets of sealing rings that prevent air flow from leaking into the air vent; An exhaust control ring prevents air flow from leaking through the vent to the isolation chamber. The exhaust control ring is basically the same as the pressure relief ring of the packing, so the form of the seal ring is its main differentiation point. Its main components are a decompression ring and a seal ring.
The role of the decompression ring is to limit or control the leakage of the gas flow, mainly to reduce the role of decompression. During the suction stroke, the rapid expansion of gas from the stuffing box is prevented from flowing back to the cylinder, the pressure of the cylinder is rapidly reduced to suction pressure, and the gas in the stuffing box has a tendency to flow back into the cylinder. If there is no throttling restriction, the seal ring will open, causing premature failure or wear of the seal ring.
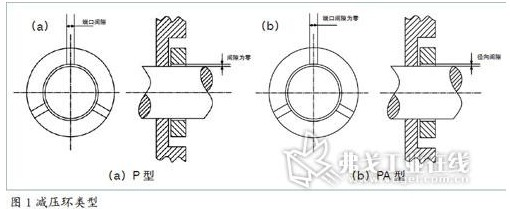
The BT-type seal ring (Figure 2) is a single-acting ring that seals only one side of the pressure. It consists of a radial slit ring (on the high pressure side) and a tangential slit ring. When the radial notch is attached to the piston rod, there is still a gap in the notch so that when the compressor is running, high-pressure gas is introduced into the packing chamber, and the high-pressure gas is used to compress the packing. In addition, the radial cut ring and the tangential cut ring use the positioning pins to determine the mutual position. In order to ensure the seal, the cuts are offset from each other by an angle to prevent the gas from passing through the packing ring, and the two sealing rings are used to prevent the sealed shaft from being attached to the plane. Leakage. In addition, in order to ensure the sealing effect of the packing rings, the two rings and the piston rod need to cooperate well.
BD-type seal ring (Figure 3) is a double-acting packing ring that can seal the pressure in two directions. It is composed of two butt-joint tangential cut rings. The gaps cover each other and use the positioning pins to determine the connection position to prevent Gas leak.
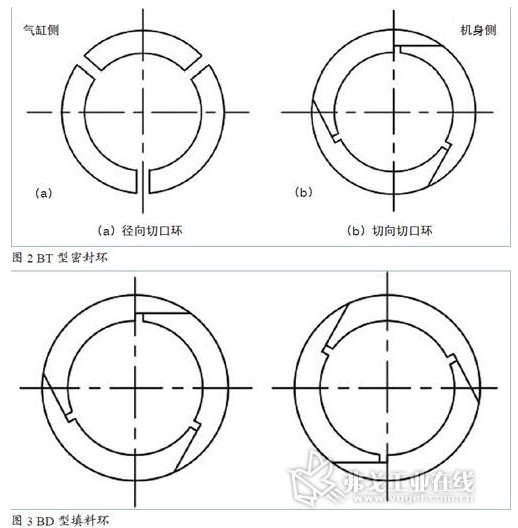
The BTR seal ring (Figure 4) consists of a non-metallic packing ring and a metal rigid ring. The BTR seal ring is suitable for high pressure compressors. The rigid ring is in the form of a radial notch. The clearance of the rigid ring port is zero. The inner diameter of the ring is slightly larger than the piston rod, and the piston rod is not tightened under the pressure (or Slightly clamping the piston rod) to prevent the non-metallic filler from being squeezed out. The role of the rigid ring is to reduce the direct impact between the tangential incision ring and the stuffing box, extending its service life. In addition, the rigid ring assists in the removal of heat from the surface of the piston rod through slight contact with the piston rod.
The TR-type seal ring (Fig. 5) is actually a variant of the BTR-type seal ring. It combines the characteristics of a tangential ring and a radial ring, which not only serves as the introduction of high-pressure gas but also serves as an axial seal. Since the tangential and radial rings are on the same ring, one leakage point can be reduced. In addition, since the seal has only two rings and the axial dimension is small, when the sealing pressure is high, the amount of leakage can be reduced by increasing the form of the stuffing box.
Seal leakage fault analysis and improvement measures
Since the inner ring of the packing ring is closely fitted to the piston rod, friction occurs between the packing seal ring and the piston rod when the device is running at a high speed, and at the same time, a large amount of frictional heat is generated, resulting in a local temperature that is too high and close to the side of the cylinder of the compressor. The temperature of the seal ring is much higher than the temperature on the body side, which can easily lead to damage of the packing seal ring and cause leakage. In order to solve the problem of seal ring failure caused by frictional heat, a part of the gas can be introduced into the surface of the piston rod by improving the sealing structure, which effectively reduces the pressure of the seal ring against the piston rod and prevents the seal ring from wearing out. In addition, the material of the seal ring is filled with PTFE, and the content of copper powder and fiber is increased in an appropriate amount to increase the heat conduction and wear resistance.
In addition to the above reasons, the leakage and improvement of packing seals mainly include the following aspects:
Packing body gasket
Packing body washers are generally made of soft metal or O-rings as gaskets. The damage of the sealing surface of the fuselage and the uneven installation force can easily cause the gasket to break, which causes the leakage of the sealing medium from the outside of the packing body to the middle body cavity. In the middle, the temperature of the middle body and the vent line increased abnormally. For the above situation, it can be eliminated by replacing parts and correct installation.
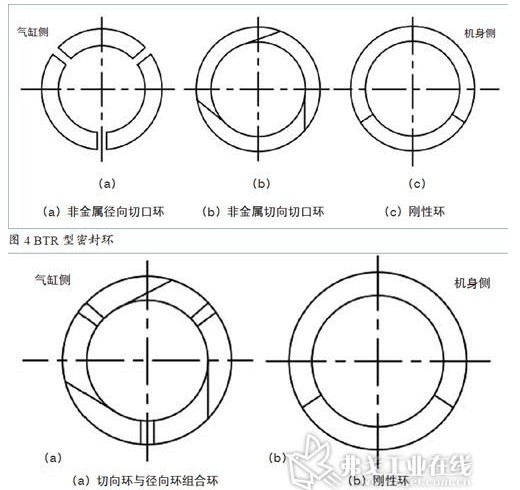
Packing box face
In the packing installation, it is required that the tangential incision ring must lie flat on the side of the groove of the stuffing box, usually due to a defect in the sealing surface of the stuffing box or a deviation of the squareness of the entire stuffing box from the piston rod, thereby causing the seal to leak. In order to avoid sealing failures in these situations, it can be solved by grinding the sealing surface of the stuffing box and adjusting the stuffing box bolts.
Packing ring
Packing ring is the most important factor causing seal leakage. Leakage of packing ring can be divided into the following aspects:
Sealing ring installed in the wrong order;
The axial gap of the seal ring is not controlled, which causes the temperature during operation to increase. The seal ring expands axially and is jammed in the stuffing box. The tangential cut-out ring seal fails.
The surface of the packing sealing ring itself is not polished satisfactorily, and the inner hole of the sealing ring and the piston rod do not fit well, resulting in leakage. Generally, the inner surface of the sealing surface can be ground to improve the fit of the sealing surface and eliminate leakage.
Sealing ring between stuffing boxes
Due to the shearing effect of the sealing ring between the stuffing boxes during installation or the aging of the sealing ring, the sealing medium gas strings are caused to cool the water and affect the sealing effect. By observing the filling cooling water sight glass, if bubbles appear, it indicates that the seal ring is defective and can be eliminated by replacing the seal ring.
Poor alignment of packing box and piston rod
When checking the leakage of the packing, the alignment problem between the stuffing box and the piston rod is often neglected. The misalignment causes a tangential incision ring and the angle between the flanks of the stuffing box to cause a leak. In order to correct misalignment between the stuffing box and the piston rod, align the piston rod with the stuffing box by adjusting the bolts of the packing body and applying appropriate torque to center the piston rod. If the concentricity between the cylinder and the slide is caused by the installation, adjust the concentricity by adjusting the cylinder support to solve the leakage problem.
The effect of external auxiliary system on the sealing effect
Cooling water
The change in temperature results in a change in the relative positions of the packing rings and piston rods, packing rings and packing boxes, packing rings themselves, which can easily cause leakage when the relative position changes. As the frictional heat causes the temperature of the packing ring to rise, the inner bore of the packing ring is deformed to disengage the piston rod, or the packing ring is separated at the tangential incision. In addition, the piston rod is curved due to uneven frictional heating, which affects the centering. In addition, when the piston rod is operated at a high temperature for a long period of time, it will exacerbate its wear and eventually lead to leakage. Therefore, it is of great significance to ensure the safe operation of the equipment by ensuring the smoothness of the cooling water of the packing and the proper flow rate.
Effect of oil injection
Too little oil in the packing seal can cause poor lubrication in the packing operation. The packing ring wears too quickly and the oil filling amount is too high. This can cause a large amount of sludge to be formed due to the worn packing and lubricant, resulting in deterioration of the lubrication condition. Therefore, the amount of oil injection must be strictly controlled.
Leakage recovery system
Leakage from the packing seal leaks through the leak recovery line. If a blockage occurs in the pipeline, it will cause the pipeline to collapse, and the leakage of the medium will be reversed, causing the leakage of the packing. Therefore, it must be ensured that the leak recovery system is unobstructed.
Medical Products High Frequency Welding Machine
We supply machinery and services to many major international companies and we have activity in the following industries:
Medical: Including Blood bags, Urine bag ,blood bag ,Colostomy bags, DVT bags, Solution bags, EVA bags, Medical Mattresses, produced on HF welding machines, high frequency welding machines, rotary and inline machinery. The materials can be PVC, Medical Grade PVC and Non PVC.
Wristband Machine,Medical Products High Frequency Welding Machine,Blood Pressure Cuff Welding Machine,Blood Pressure Cuff Making Machine
Hangzhou Xiaoshan Wanfeng Mechanical & Electrical Equipment Factory , https://www.wanfengmachinery.com